EDIT: please, see my next post below for fixes of basic flaws of the suggested in this post ideas.
Because continuous welded rails are more expensive to lay than ordinary jointed track and can result in rail buckling during extreme summer heat, why not use some of joining techniques, listed below.
1) First, why not use more often the diagonal expansion joint, shown on the picture below (from Wikipedia)?
2) My idea for an "overpass" rail.
For this we need a double sided wheel set like this:
This is how the track looks from the top:
And the side view of the track joint:
Of course, the climb of the "overpass" rail doesn't have to be so steep and high as in the picture. It's just for the illustration of the concept.
It seems to me, that the double sided wheel set, shown on the picture above, won't cause any trouble at railroad switches, as the inner side of the wheel is at the same level as the outer (usually running) side of the wheel.
The extra weight of the wheel set (due to the addition of the inner side), probably won't cause too much extra energy loss (if any at all).
3) Another simple idea about an "overpass plate cover" of a rail joint:
Certainly, the plate is properly attached to the joint and not just falling off the rails.
So, what do you think of it?
P.S.: Just asking and suggesting. Not saying the "final truth" and "everyone must implement this". Nothing of the sort. If you think the ideas are not viable, just say why and that's all.
Please, reply if anyone has any interest in this
Because continuous welded rails are more expensive to lay than ordinary jointed track and can result in rail buckling during extreme summer heat, why not use some of joining techniques, listed below.
1) First, why not use more often the diagonal expansion joint, shown on the picture below (from Wikipedia)?
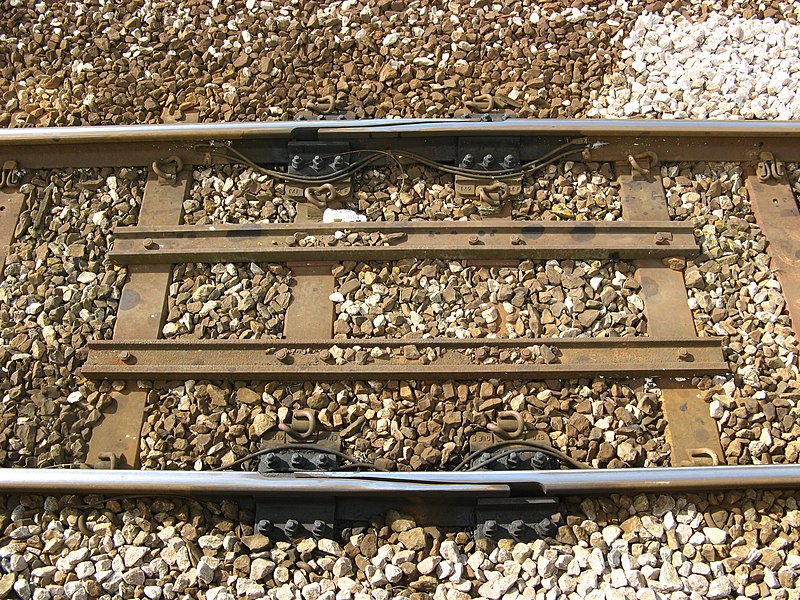
2) My idea for an "overpass" rail.
For this we need a double sided wheel set like this:
This is how the track looks from the top:
And the side view of the track joint:
Of course, the climb of the "overpass" rail doesn't have to be so steep and high as in the picture. It's just for the illustration of the concept.
It seems to me, that the double sided wheel set, shown on the picture above, won't cause any trouble at railroad switches, as the inner side of the wheel is at the same level as the outer (usually running) side of the wheel.
The extra weight of the wheel set (due to the addition of the inner side), probably won't cause too much extra energy loss (if any at all).
3) Another simple idea about an "overpass plate cover" of a rail joint:
Certainly, the plate is properly attached to the joint and not just falling off the rails.
So, what do you think of it?
P.S.: Just asking and suggesting. Not saying the "final truth" and "everyone must implement this". Nothing of the sort. If you think the ideas are not viable, just say why and that's all.
Please, reply if anyone has any interest in this

Attachments
Last edited: